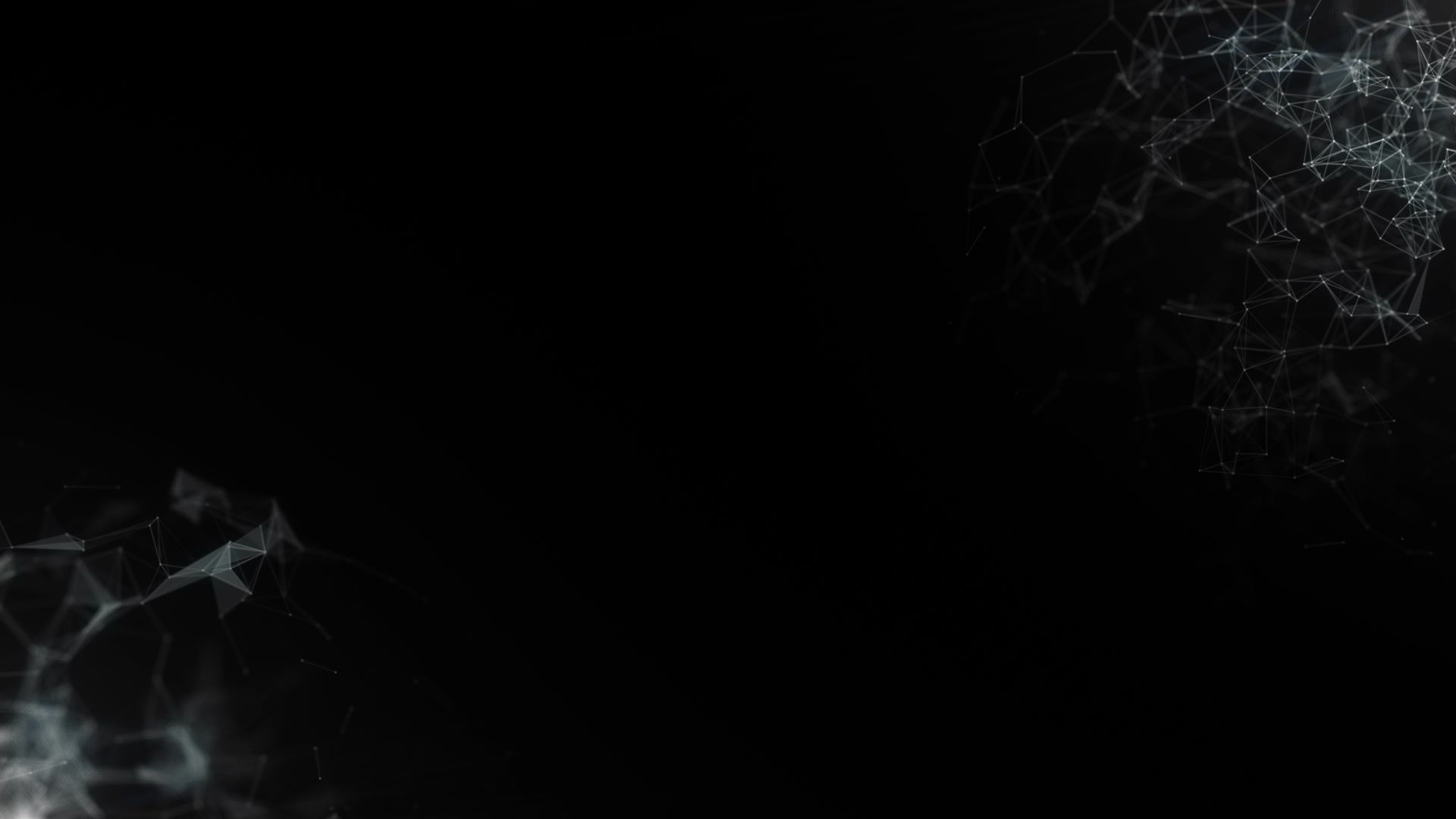
Bottlenecks in Current MEMS Design Flows : From White Papers - IntelliSense
​
We can classify bottlenecks in MEMS design according the different stages of the design evolution. The major bottlenecks in current MEMS design methodologies include : Process information, High-fidelity models, Limited libraries, favorite toolset, Co-simulation with other system simulators, Layout tools, High quality layout automation, Geometry manipulation and meshing, Parametric meshing, Incorporation of process corners into physical design, Process flow modeling, Integrated cost and economics modeling, Deep Silicon Etch Simulations, Incorporating accurate process details into meshes, Enhanced ROMs, Parametric ROMs, More.
Dry Etching of Silicon is just Trench Making.
​
Deep Reactive Ion Etching (DRIE, or the Bosch process) enables the fabrication of high aspect ratios by repeating deposition and etching cycles. Every cycle can be broken down into three stages: (i) isotropic polymer deposition (driven by neutral radicals), (ii) strongly-directional polymer removal (driven by charged ions accelerated vertically), (iii) ion-driven (vertical) + radical-driven (isotropic) silicon etching. More.
MEMS/CMOS Layout Editor - BluePrint
​
When you think about it, MEMS layout is one of the most cumbersome parts of the design process, involving countless revisions, incompatible data formats and minute details. The challenges of MEMS layout are compounded further by the fact that most tools available are IC layout tools, or less-appropriately, architectural design tools.
​
Blueprint is the first layout tool designed specifically for the MEMS community. Our goal with Blueprint was to revisit the workflow of the layout engineer and create a tool that would be effortless to learn and use. Our design philosophy for Blueprint is: "simple things should be simple, complex things should be possible." That‘s why our product provides configurable palettes that you can drag and customize to your needs; clearly illustrated icons; and configurable grids and guides - all of which make device layout easier than ever. We even went a few steps further... automatically linking masks created in Blueprint to process steps for creating 3D visualization of your device. What’s more, Blueprint users can now link the layout with automatic mesh creation and refinement for device-level analysis! More.
1. Microloading (loading effect) and DRIE-lag (ARDE) simulation
2.Blueprint-- Professional Mask Editor
3.Fast simulations that match the experiments
4.Extensive database
5.High-index off-cut substrates beyond standard wafer orientations and flats
6.Different etch rates for Si(111) depending on the inclination angle
6. Different etch rates for Si(111) depending on the inclination angle
7. Characterize your etchant to understand how it etches
8. Convex corner undercutting and compensation
9. Complex processing with multiple etching steps
10. Submicron, nanoscale etching
11. Diffusion-limited isotropic etching
12. Up to three cross-sections with geometrical measurements
12 Reasons to Use IntelliSuite Clean Room Tools
Simulating Piezoelectric material on Sloped Plane
​
The piezoelectric effect is the linear electromechanical interaction between the mechanical and electrical state in crystalline materials. The piezoelectric constant is rigorously defined using tensor analysis. Thus, the orientation of the piezo crystal material is very important to the piezoelectric analysis. Here we present an interesting case wherein the piezo material is on the angled walls (Fig 1). To accurately simulate this device, we need to model the piezo material property with the local angle information and anisotropic piezoelectric material property for each angled structure.. More.
Micromachine Energy Harvesting Device for EM Application
At present, harvesting vibration energy from the environment is an attractive alternative power source for low power wireless sensing applications. Our example on the non-linear model provides insights about the hybrid frequency broadening (HFB) by capturing the energy due to different modes of vibration through a fixed-fixed beam.